Is there an art form that whispers rather than shouts, that offers a tactile experience as much as a visual one? Debossing, a technique often overshadowed by its more flamboyant sibling, embossing, offers precisely that: a quiet elegance, a subtle depth that elevates design and material in a way that speaks volumes without uttering a word.
The world is filled with methods designed to make an impression, but debossing provides a more intimate connection. While embossing raises a design, debossing subtly presses it inward, creating a sunken relief that draws the eye and the touch. This understated approach finds its strength in its discretion, allowing for sophisticated branding, refined packaging, and a sense of quality that speaks to a discerning audience. This is the hallmark of a process that transforms a surface, adding visual interest and tactile dimension through a delicate dance of pressure and form.
The process of debossing, at its core, is a remarkably precise one. It begins with the creation of a die, a critical tool that acts as the negative image of the desired design. This die, often crafted from metal, is then paired with a counter die. The substrate, the material to be debossed be it paper, cardstock, leather, or even certain plastics is placed between these two mating parts. The die then applies pressure, forcing the material into the cavity of the die and creating the recessed impression. The success of the debossing hinges on the precision of the dies, the pressure applied, and the properties of the material itself. Each element must be carefully calibrated to ensure a clean, sharp, and lasting impression.
- Unlock The Future Remote Iot Behind Router Android Free Solutions
- Hdhub4you The Ultimate Guide To A Popular Movie Streaming Platform
Now, let's delve into the technical aspects, the mechanics behind this intriguing process. The process starts, as it does with many forms of printing and surface treatment, with a design. This design, initially created in a digital format, is then translated into a physical die. The die is the heart of the debossing process, the tool that will ultimately create the sunken image. The manufacturing of a die often involves highly specialized processes, including machining, etching, or laser cutting. The choice of method depends on the complexity of the design and the desired level of detail.
The die is carefully mounted into a debossing machine, which is typically equipped with a pressure mechanism. The substrate, the material to be debossed, is then placed between the die and a counter-die, which provides support and a smooth surface for the impression. Precise alignment is critical to ensure accurate registration of the debossed design. The debossing machine applies pressure, forcing the substrate into the cavity of the die, creating the recessed impression. The pressure and time of application need to be finely tuned, to achieve the right depth and detail without tearing or damaging the material.
There is more that meets the eye. The debossing process demands careful consideration of material selection. Paper, for example, is a popular choice, especially for stationery, business cards, and packaging. The weight, texture, and composition of the paper significantly impact the final result. Thicker paper will typically hold a debossed impression more sharply and clearly than thinner paper. The fiber direction of the paper must also be considered to avoid cracking or splitting during the debossing process.
- Why Did Gloria Gaither Stop Singing Exploring The Legacy Of A Gospel Icon
- Access Pi Remotely Tutorial A Comprehensive Guide To Connecting Your Raspberry Pi From Anywhere
Beyond paper, a range of other materials can be debossed, each with its own unique challenges and opportunities. Leather, for instance, debosses beautifully, adding a touch of luxury and sophistication to wallets, journals, and other leather goods. The natural grain of the leather adds an interesting texture to the debossed design. However, the depth of the deboss must be carefully controlled to avoid tearing the leather, and the tooling must be carefully selected to match the leather type.
Plastics present another avenue for debossing. Various plastic materials can be debossed, offering a versatile solution for product branding, labeling, and decorative elements. However, the temperature and pressure must be carefully controlled to prevent warping or cracking. Metal, although less common, can also be debossed, particularly for creating recessed designs on nameplates or plaques. This requires highly specialized equipment and expertise.
The application of debossing is vast and varied, offering potential across a wide range of industries. In the realm of printing, debossing is frequently used for creating tactile effects on book covers, brochures, and packaging. It allows for the creation of a sophisticated and memorable presentation. In the design of corporate stationery, a debossed logo or brand name can add a touch of elegance and professionalism to business cards, letterheads, and envelopes. This subtly enhances the brand's visual identity.
When it comes to product packaging, debossing enhances the appeal of high-end products. Luxury goods manufacturers, from cosmetics to spirits, often employ debossing to create a sense of quality and exclusivity. In the realm of branding, debossing is a useful way of conveying a brands values. A debossed logo on a promotional item, such as a notebook or pen, adds a touch of sophistication and elevates the perceived value of the promotional materials. Debossing is also important in the creation of invitations and announcements, adding a formal and elegant touch to the design. In general, debossing allows for a unique tactile experience.
Consider the realm of bookbinding, where debossing is applied to create visually appealing covers. The technique, giving a three-dimensional depth to the surface of books, elevates a basic cover into something much more appealing, tactile and engaging. The result is a more memorable and desirable object, encouraging readers to hold onto the book and keep the material with them longer.
Let us now consider the steps to achieve such a finish. The process, though elegant in its results, is a carefully orchestrated series of steps. It begins with the design. The design is the foundation upon which the entire debossing process is built. This design, be it a logo, a pattern, or simply text, is created using specialized graphic design software. The designer must consider the material on which the design will be applied, as well as the desired visual effect. The design must be converted into a suitable format for the manufacturing of the die.
This leads us to the next stage: die creation. The die, as mentioned earlier, is the heart of the debossing process. It is a custom-made tool that acts as the negative of the design. It is the die that presses the image into the substrate, or material. The die can be made of various materials, including metal, wood, or plastic, depending on the material being debossed and the required level of detail. The manufacturing process involves highly specialized techniques, such as etching, machining, or laser cutting. This involves transferring the design from the digital format into the die.
We then move to the important step of material selection. The choice of material is critical to the success of the debossing process. The material will be debossed and greatly affects the final appearance of the debossed design. Paper, leather, and various plastics are all popular choices, each of which provides its own unique advantages and challenges. Consideration must be given to the thickness, texture, and composition of the material. The type of material greatly influences the tooling and pressure needed for the debossing.
Then there's the crucial process of die mounting. The die is then carefully mounted into the debossing machine, which is a specialized press that applies pressure to the die and the substrate. The machine will be adjusted for the type of material and design. Precise alignment of the die is critical to ensure accurate registration of the debossed design. The mounting must be carefully calibrated to ensure even pressure distribution across the design. This directly affects the quality of the final product.
The next step is the debossing itself. Once the die is in place and the substrate is in position, the debossing process begins. The debossing machine applies pressure to the die, forcing the substrate into the die cavity, creating the recessed impression. The amount of pressure, the dwell time, and the temperature (if applicable) must be carefully controlled to achieve the desired effect. The pressure and the material must be carefully regulated to prevent the material from tearing or splitting. The settings are dependent upon a wide range of factors, including the material and the type of design. The success of this step is evident in the final look.
Finally, we arrive at inspection and finishing. After the debossing is complete, the finished product must be inspected to ensure it meets the required quality standards. Any imperfections or defects must be identified and corrected. Then the finish is given. This includes the application of additional treatments, such as foil stamping, spot UV coating, or other embellishments. These finishing touches can further enhance the visual appeal and tactile experience of the debossed design.
In essence, the debossing process is a carefully orchestrated process. It involves the intersection of design, die creation, material selection, and careful execution. The results are elegant, and often understated, but always impactful.
In contrast to embossing, debossing involves pressing a design or pattern into a material, creating a depressed or sunken effect. This technique adds a subtle yet refined touch to various objects, elevating their visual appeal. Debossing follows a similar process to embossing but with a reverse effect. The steps involved are as follows: Debossing refers to a design that has been pressed into a substrate so that the resulting image is recessed lower than the surrounding surface. Just like embossing, the debossing process uses a die system with two mating parts. However, the process is reversed. Embossing and debossing are the processes of creating either raised or recessed relief images and designs in paper and other materials. An embossed pattern is raised against the background, while a debossed pattern is sunken into the surface of the material but might protrude somewhat on the reverse side.
While debossing might seem straightforward on the surface, the reality is that achieving a beautiful, well-executed deboss is an art in itself. There are several common challenges that debossers face, which, if addressed appropriately, can affect the final result. One of the biggest problems is the proper selection of the die. The die must be of the right material, the right size and must have sharp detail. Any flaws will show in the final product. A second challenge is material compatibility. It is crucial to select the right material that will accept the debossing process. The wrong material can tear, split, or otherwise damage, so the careful selection of material is a key element.
Pressure and temperature play a huge part in the debossing process. The pressure is applied to the die must be finely tuned to achieve the desired depth without damaging the material. Too much pressure, and the material can tear, or cause the surrounding surface to become distorted. Too little pressure, and the deboss will be too shallow. In some instances, heat is used in addition to pressure, which adds another element of control. The temperature must be controlled to ensure that the materials do not warp.
Alignment also plays an important part. Precise alignment of the die and the substrate is critical to ensure that the debossed design is correctly positioned. Any misalignment will result in a blurred or uneven image, destroying the desired visual effect. Another challenge is depth control. Achieving the proper depth is important to produce the correct level of detail. Careful adjustments to the pressure and tooling are needed to achieve the desired depth. Depth and alignment are closely interrelated, and any deviation in one area will negatively affect the overall impact. A final element is the consideration of finishing touches. The debossing is rarely an end in itself, because often additional treatments will be added to enhance the visual effect, such as color. The finishing touches require experience to complete.
Several case studies are presented that show the merits of a debossing approach. Many companies and designers are increasingly realizing the power of this often understated technique. From luxury brands to small businesses, debossing is finding a place in a wide variety of applications.
In essence, debossing offers a different approach for branding and design. This is a technique that should be embraced by any designer, brand or product seeking to add a sophisticated and elegant touch. It is the difference between a design that is noticed, and one that is experienced. It offers the potential to elevate a project to another level, enhancing its value and providing a lasting impression. It is a process that rewards careful consideration and expertise, which delivers results that will both fascinate and impress.
- Free Download Ssh Remote Iot Device Raspberry Pi The Ultimate Guide
- Best Remote Access Iot Device Ssh A Comprehensive Guide To Secure Connections
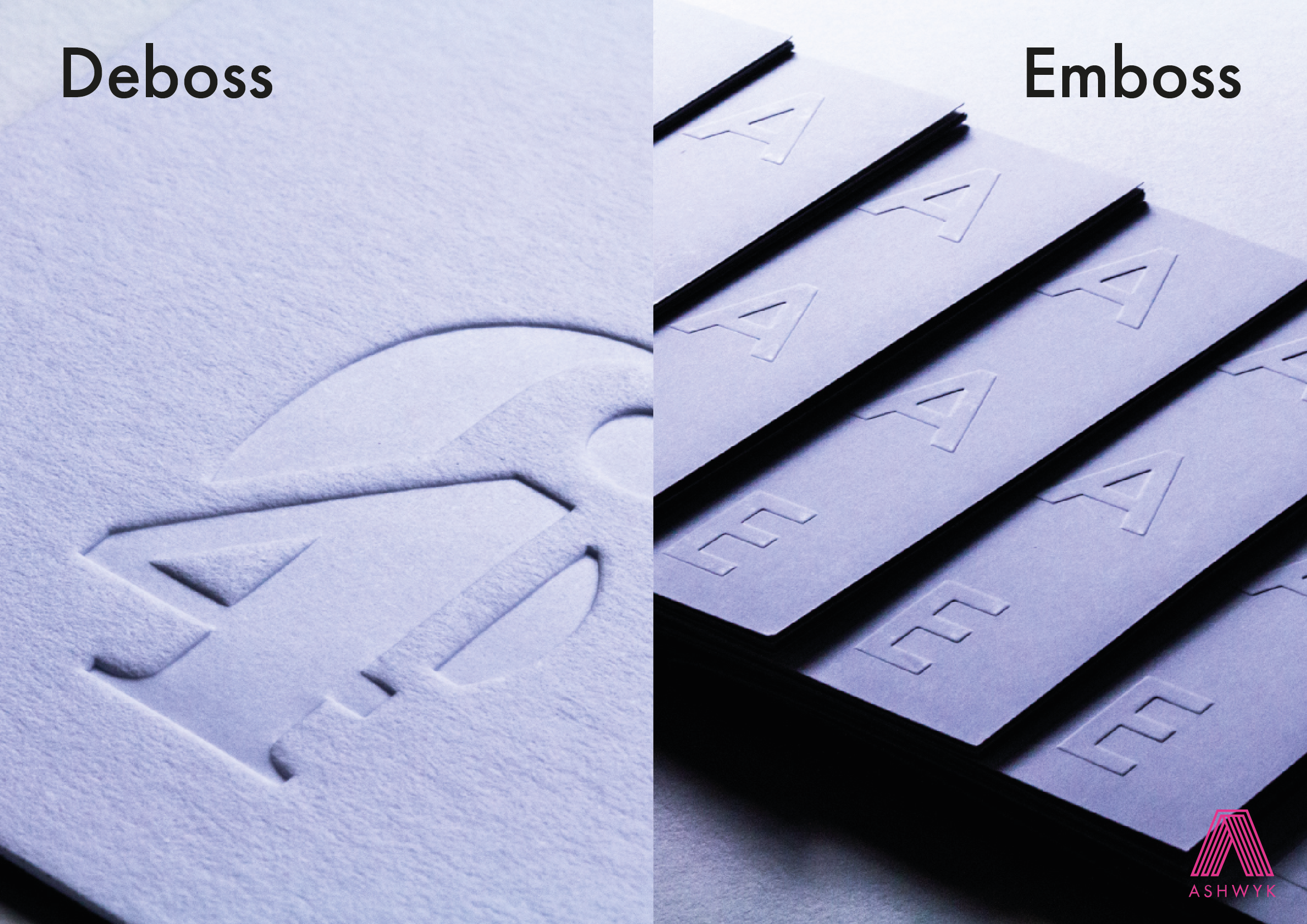

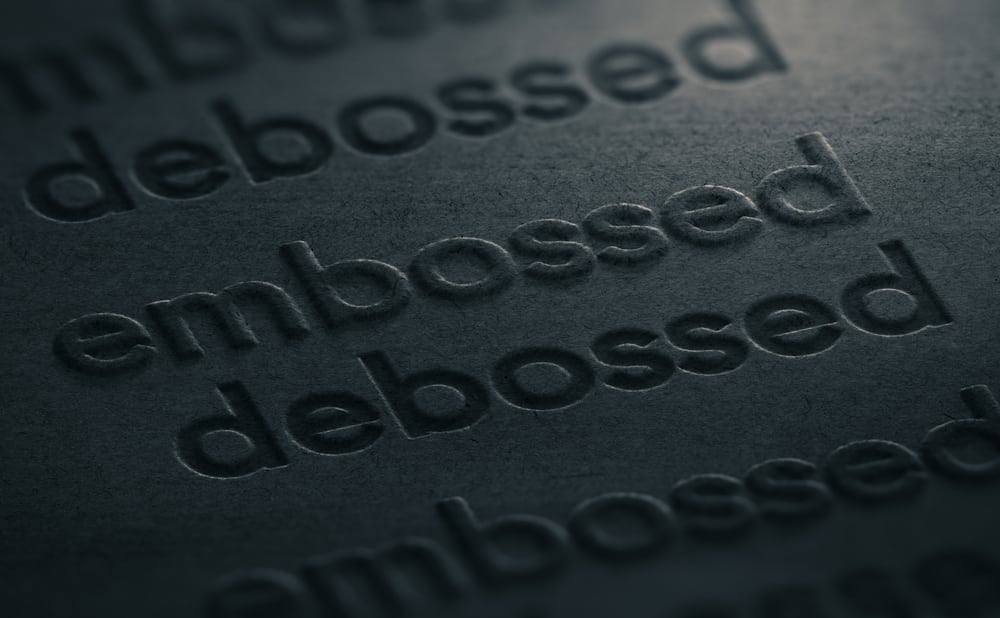