Is precision engineering a science, an art, or a crucial blend of both? The ability to achieve exacting tolerances, particularly in the demanding realm of deep hole drilling, hinges on meticulous planning, advanced technology, and a deep understanding of the materials and processes involved.
The quest for precision in manufacturing often leads to specialized techniques, and deep hole drilling stands as a prime example. Unlike conventional drilling, which can be relatively straightforward, deep hole drilling presents a unique set of challenges. These challenges stem from the depth of the hole, the need for precise alignment, and the critical role of coolant in the process. The application of cooling lubricant is not just a minor detail; it becomes a vital aspect of the operation, a necessity that dictates the success or failure of the entire endeavor. The pressure and quantity of this lubricant must be carefully managed, a factor that separates the professionals from the novices. It is this attention to detail, this intricate dance between tool and material, that defines the excellence in modern manufacturing.
Name | TBT Tiefbohrtechnik (Focus on Deep Hole Drilling) |
Company | Part of the internationally active Nagel Group |
Industry | Manufacturing, Precision Engineering |
Specialization | Deep Hole Drilling Solutions and Contract Manufacturing |
Key Technologies |
|
Key Services |
|
Core Competency | Precision drilling of deep holes with precise diameter tolerances. Managing deep-hole drilling under pressure. |
Location | Not specifically stated, but part of an international group. |
Noteworthy Aspect | Direct Deployment capabilities for contract manufacturing, enabling swift and effective project completion. |
Reference Website | Nagel Group Website (This website is a placeholder for a real Nagel Group resource - the actual TBT information may reside within the broader Nagel Group structure.) |
Deep hole drilling, a critical process in manufacturing, necessitates a precision-driven approach, differentiating itself from standard drilling methods. The fundamental difference arises from the depth of the hole, demanding specialized techniques to maintain accuracy and quality. The challenge includes intricate factors such as achieving precise alignment, material selection, and maintaining the integrity of the drilled hole. The design of the drilling equipment and selection of materials are equally vital, which adds to the complexity of the task.
- How To Manage Remote Iot Devices With Free Download Solutions
- How To Remotely Access Raspberry Pi For Remote Iot Projects Free Guide
One of the primary distinctions lies in the coolant. The coolant used is a critical element of the deep-hole drilling process, particularly in contrast to standard drilling operations. The coolant performs multiple critical roles: reducing friction, carrying away heat generated during drilling, and flushing away chips. The coolants function ensures the efficiency of the operation, and the lifetime of the drill used, to be as prolonged as possible. In deep-hole drilling, the volume of cooling lubricant must be significant, and the pressure must be high, and also it must be kept at the proper parameters to ensure the success of the drilling operation.
The tools of the trade further emphasize the specialized nature of this process. Symmetrical twist drills, often right-handed, are commonly used in deep hole drilling. The design of these drills is engineered to effectively remove material from deep within the workpiece, while maintaining hole straightness and diameter accuracy. The drill design, material, and geometry play pivotal roles in the performance. It is essential that the design is robust and appropriate for the application, as a malfunction in the drill will cause issues in the finished product.
The term "\u2113 3 tolerance of diameters \u00f8d tolerance" refers to the level of precision. The "tolerance" refers to the permissible variation in the diameter of the drilled hole. A tighter tolerance, such as "\u2113 3," signifies a higher degree of accuracy. This level of precision is often critical in applications where the drilled holes serve as passages for fluids, the assembly of precision components, or other applications where exact dimensions are required. Managing such tolerances requires careful control over all aspects of the drilling process, from machine setup to tool selection to coolant management.
- Miaz The Rising Star In The Music Industry
- Remoteiot Platform Ssh Free The Ultimate Guide To Secure And Seamless Remote Access
The Nagel Group, with its international reach, provides a framework for TBT Tiefbohrtechnik to operate and deploy its specialized services, including deep-hole drilling and contract manufacturing. The Group's influence may extend to the support systems for research and development, marketing, and the management. This structure allows TBT to focus on its core competencies while benefitting from the resources and expertise of the larger organization. The Group's business framework contributes to TBT's ability to meet the complex demands of its clients.
Contract manufacturing plays a vital role in the precision engineering landscape. It provides an effective solution for businesses that require deep hole drilling but may not have the in-house capabilities or resources to perform this specialized task. Direct deployment in contract manufacturing enables the rapid implementation of solutions, and it facilitates efficient project turnaround times. The approach also offers access to specialized expertise, state-of-the-art equipment, and the assurance of quality that comes from working with experts in the field. This arrangement contributes to the overall efficiency and competitiveness of the industry.
The entire process requires a delicate balance of technical expertise and operational efficiency. It also involves strategic considerations related to material properties, cutting speeds, and machine settings. The selection of cutting tools, the choice of cutting fluids, and the precision of the machines are very important. The team must have the proper training and experience in order to deliver consistent results.
In conclusion, deep hole drilling is more than just a process; it is a specialized skill that requires both precision and adaptability. The need for tight tolerances, as defined by terms such as "\u2113 3," underscores the importance of the meticulous attention to detail, coupled with a thorough understanding of materials science and engineering principles. The utilization of specialized equipment, like symmetrical twist drills, and sophisticated coolant systems, is what separates the professionals from the amateurs. Ultimately, the success of deep hole drilling reflects an unwavering commitment to excellence in precision manufacturing.
The reliance on contract manufacturing reflects a move toward specialization and efficiency in the manufacturing industry. Direct deployment within this framework emphasizes the importance of quick project completion and flexibility in meeting the complex demands of the market. The involvement of companies like TBT Tiefbohrtechnik, with backing from larger groups such as the Nagel Group, indicates a future that is shaped by technological advancements and a constant focus on high standards.
In the world of precision engineering, the quest for perfection continues. The ability to drill deep, accurate holes is a testament to the power of specialized technology, combined with a dedication to achieving exacting standards. The successful execution of this task is more than simply a technical accomplishment, it embodies the spirit of innovation and a commitment to excellence that drives the industry forward.
- Emma Anturin The Rising Star In The Music Industry
- Management Of Raspberry Pis Remotely With Remote Iot Management Platfo
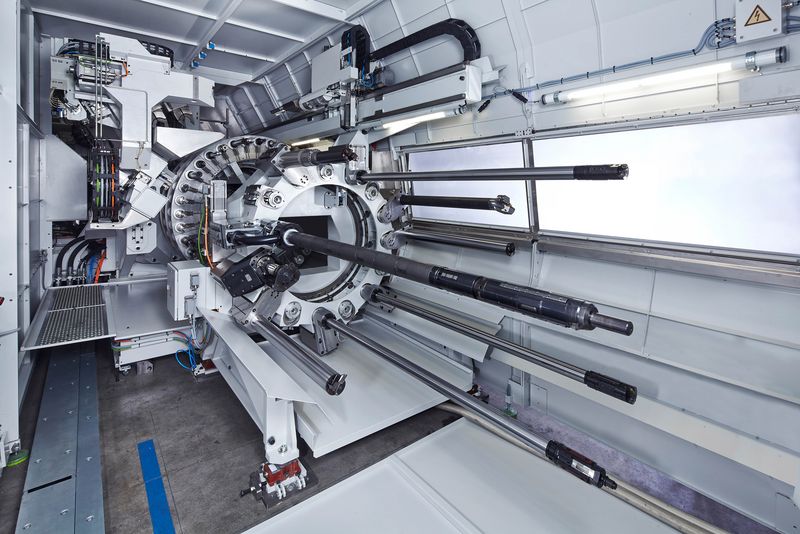

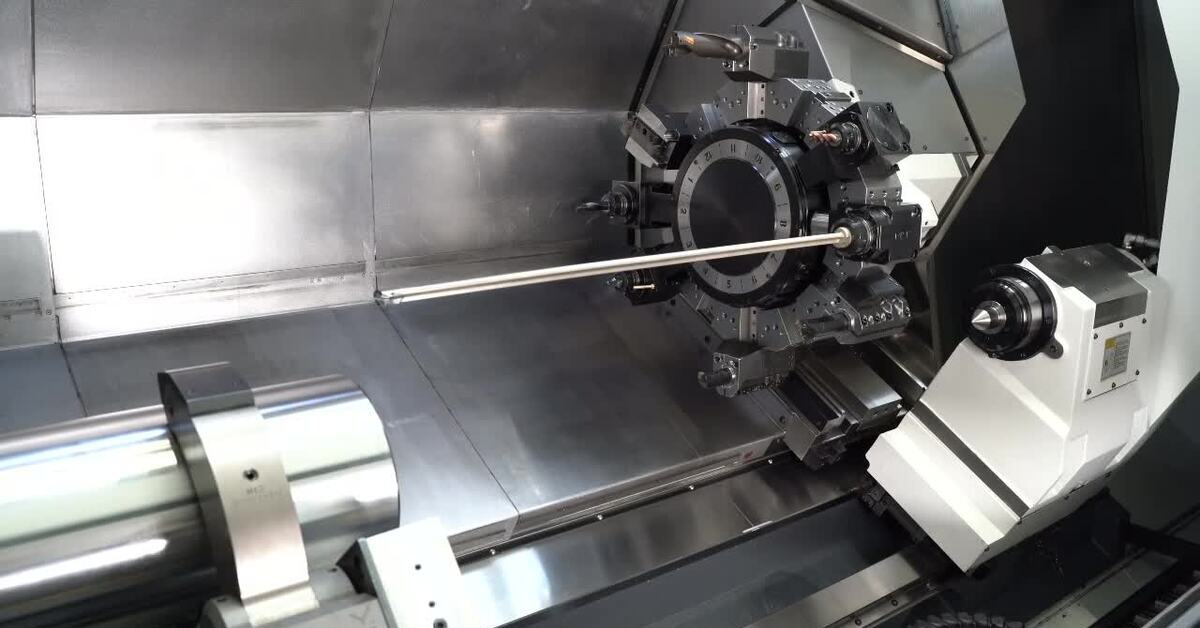