Could Direct-to-Film (DTF) printing be the revolutionary printing technique you've been searching for to elevate your creative projects? DTF printing offers a vibrant, durable, and versatile method for transferring designs onto a wide range of fabrics, opening up exciting possibilities for customization and personalization. This innovative technology has quickly gained traction, becoming a favorite among businesses and hobbyists alike, promising unparalleled quality and flexibility.
Unlike traditional printing methods, DTF printing doesn't require pre-treatment of the fabric, making the process more streamlined and cost-effective. Designs are printed onto a specialized film, followed by the application of an adhesive powder. This powder acts as the binding agent, ensuring that the ink adheres seamlessly to the fabric during the final heat transfer process. The result is a high-quality, long-lasting print that can withstand repeated washing and wear, making it ideal for everything from custom apparel to promotional items.
While specific individuals aren't directly addressed in the provided information about DTF printing, the technology has significant implications for various players in the creative and manufacturing landscape. Therefore, instead of a personal bio, here's a table highlighting the key aspects and impact of this technology, suitable for easy insertion into a WordPress environment:
- How To Use Ssh Remote On Mac For Free A Comprehensive Guide
- Understanding The Imskirby Dog Incident A Comprehensive Analysis
Aspect | Details |
---|---|
What is DTF Printing? | A printing technique that involves printing designs onto a special film, applying adhesive powder, and transferring the design onto fabric using a heat press. |
Key Benefits |
|
Process Overview |
|
Target Applications |
|
Materials Required |
|
Potential Challenges |
|
Advantages over other methods |
|
Industry Impact |
|
DTF printing allows for the creation of stunning, detailed prints on a wide array of materials. The vibrancy and resilience of the final product are noteworthy, setting it apart from alternative methods. The lack of need for fabric pre-treatment is a game-changer, making the process faster and more user-friendly. But what specifically makes DTF print unique? It lies in its ability to produce high-quality images on a diverse range of textiles. Unlike direct-to-garment (DTG) printing, which often requires special pre-treatment and works best on cotton, DTF can print on polyester, blends, and even certain synthetic materials.
The DTF process begins with a digital design. This design is then printed onto a special PET film using a DTF printer, which uses unique inks designed to bond with the adhesive powder. This specialized ink is crucial, ensuring that the colors remain vivid and do not bleed during the transfer. Next, a fine adhesive powder is applied to the printed film. This powder is the key to bonding the design to the fabric. Excess powder is removed, and the film is then either heated to cure the adhesive or immediately pressed onto the material.
The final step involves the use of a heat press. The film, with the adhesive-coated design, is placed onto the fabric, and heat and pressure are applied. The heat activates the adhesive, causing the ink to transfer from the film onto the fabric. Once cooled, the film is peeled away, leaving the printed design firmly bonded to the material. This method ensures a durable and vibrant print that can withstand washing and wear. It allows for flexibility in design complexity and material choice, a winning combination for those looking for a print solution.
- Sone 385 A Comprehensive Guide To The Iconic Fashion Brand
- Best Ssh To Iot Device For Raspberry Pi Free Your Ultimate Guide
The process of DTF printing itself is relatively straightforward, making it accessible to both novice and experienced printers. But, like any technology, its critical to comprehend the nuances to consistently achieve excellent results. First, the quality of the design file directly impacts the final print quality. High-resolution images and vector graphics are optimal for ensuring sharp, detailed prints. Next, proper printer settings and ink calibration are crucial. Ensuring the right amount of ink is applied to the film avoids issues like ink bleed or insufficient color saturation. The selection of the correct DTF film and adhesive powder is equally important. Using high-quality materials ensures better adhesion and print durability.
The application of the adhesive powder demands precision. The powder needs to be applied evenly to ensure that all of the ink on the film is covered and ready for the heat press. Excess powder should be removed, as it can affect the final print quality. The curing stage, which may involve heat or other methods, solidifies the adhesive powder. This step is crucial for ensuring that the design is firmly bonded to the fabric during the heat transfer. The correct temperature and pressure settings are also crucial, as these control the way the print adheres to the fabric. Over or under-pressing can lead to issues with the transfer quality. Selecting the appropriate fabric and preparing the material will also improve your final print.
The impact of DTF printing extends well beyond just the printing of t-shirts. Its versatility makes it suitable for a wide range of applications, from custom apparel to promotional products. Small businesses and entrepreneurs are leveraging DTF to create unique, personalized items that appeal to consumers. Whether you are printing on cotton, polyester, or blends, DTF offers excellent results. The ability to print complex, full-color designs with gradients and fine details is a significant advantage over methods like screen printing. This adaptability makes DTF a valuable tool for businesses seeking to offer a diverse product range.
One of the most significant advantages of DTF printing is its ability to print on a variety of fabrics. DTFs versatility opens up a world of possibilities for businesses. Unlike DTG, which is often limited to cotton, DTF can successfully print on polyester, nylon, silk, and blended fabrics. This makes DTF ideal for custom apparel, promotional items, and various other applications. Another benefit of DTF is its durability. Prints produced using DTF technology are highly durable and can withstand numerous washes. The print quality remains vibrant and does not crack or peel, guaranteeing that the products retain their appeal over time. For businesses, the durability translates to happy customers.
The process also offers time-saving benefits. DTF printing does not require pretreatment, which simplifies the process. The time saved on these processes can translate to faster production times and more opportunities for customization. DTF also offers low-volume printing capabilities. This is a great advantage, as it allows businesses to print small batches or even one-off designs. This on-demand capability helps reduce inventory costs and gives businesses the ability to respond quickly to custom orders. The combination of versatility, durability, ease of use, and cost-effectiveness solidifies DTF printing's place as a critical technology in modern printing.
Compared to other printing methods, DTF stands out in several aspects. Traditional methods like screen printing require a specific setup for each design, making them unsuitable for small-batch or custom orders. Screen printing also demands longer lead times and higher minimum order quantities. DTG printing offers more versatility regarding fabrics and the ability to print complex designs. However, DTG often requires pre-treatment of the fabric and is typically limited to cotton. DTF, on the other hand, can print on a broader range of fabrics and doesnt need pre-treatment, making it faster and more cost-effective. Dye-sublimation, which is often preferred for prints on polyester, does not offer the same versatility for fabric choice, and may not work as well with dark-colored fabrics.
The DTF printing market continues to grow. With more advancements in technology, we can anticipate further improvements in print quality, ink formulation, and equipment efficiency. The trend towards personalization and customization is also driving demand for DTF solutions, as small businesses and individuals seek new ways to create unique products. The future of DTF printing is bright. As the market evolves, DTF printing will continue to play an integral role in the print industry. The growing accessibility of DTF equipment, combined with its ease of use and cost-effectiveness, creates new opportunities for creative and commercial applications. These advances will likely lead to greater efficiency, higher print quality, and more sustainable printing practices.
For further information, the resources are listed below.
Google Search for DTF printing
- Unlocking The Power Of Remoteiot Vpc Your Ultimate Guide
- Setting Up Remoteiot Vpc Ssh For Raspberry Pi On Aws A Comprehensive Guide
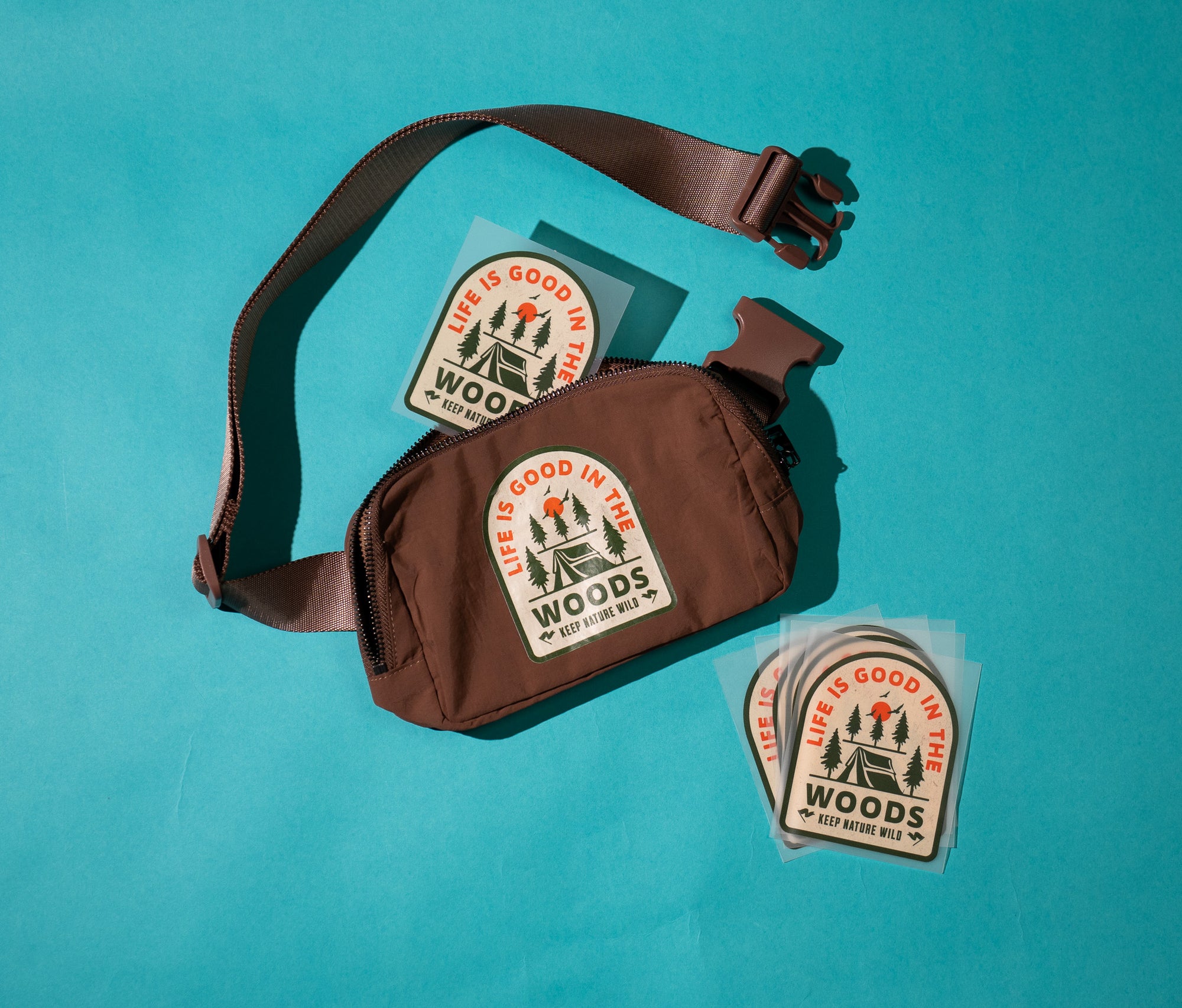
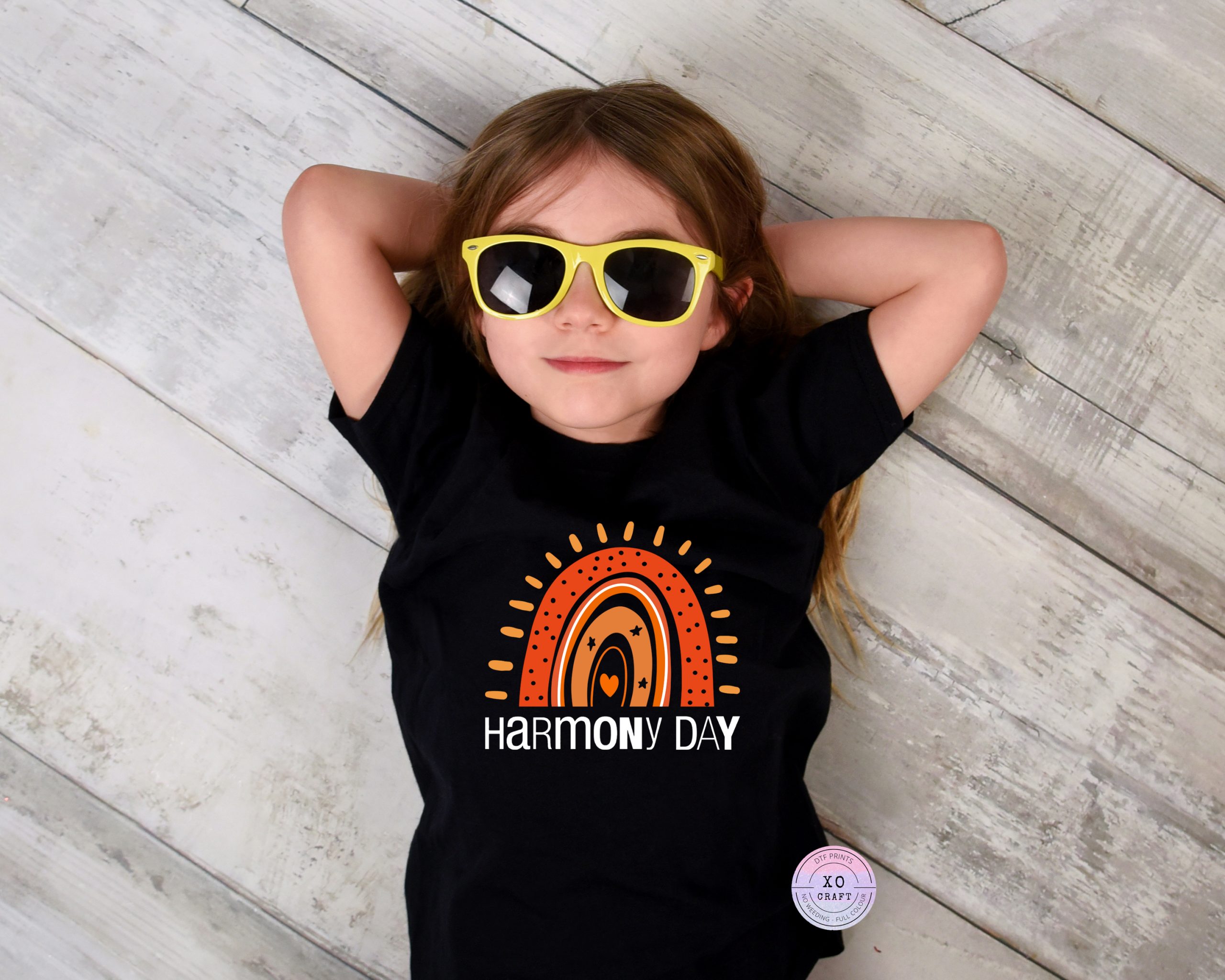
